About the Class
In his global class, Neill expanded on the content of the local class, which introduced us to the Trotec 400 laser cutter and the Roland CAMM vinyl cutter. This included preparation of files for the two machines, pre-print routines and mechanical aspects, such as safety measures and material considerations.
Building a lighting edge sign
For my personal homework project, I decided to build a glowing edge light sign. It features a box, housing a LED strip and power supply, together with an engraved sheet of acrylic. By lighting the acrylic sheet from below, the engraved motive on the acrylic plate appears to be glowing. Using the Trotec 400 laser cutter, I manufactured the press-fit parametric box from 2,5mm MDF plates. As the time slots were heavily compressed when using the laser cutter, the acrylic sign was not manufactured on that day. Instead, I cut the acrylic sign in the subsequent week. For time reasons, I omitted the Grasshopper-generated background design on the sign.
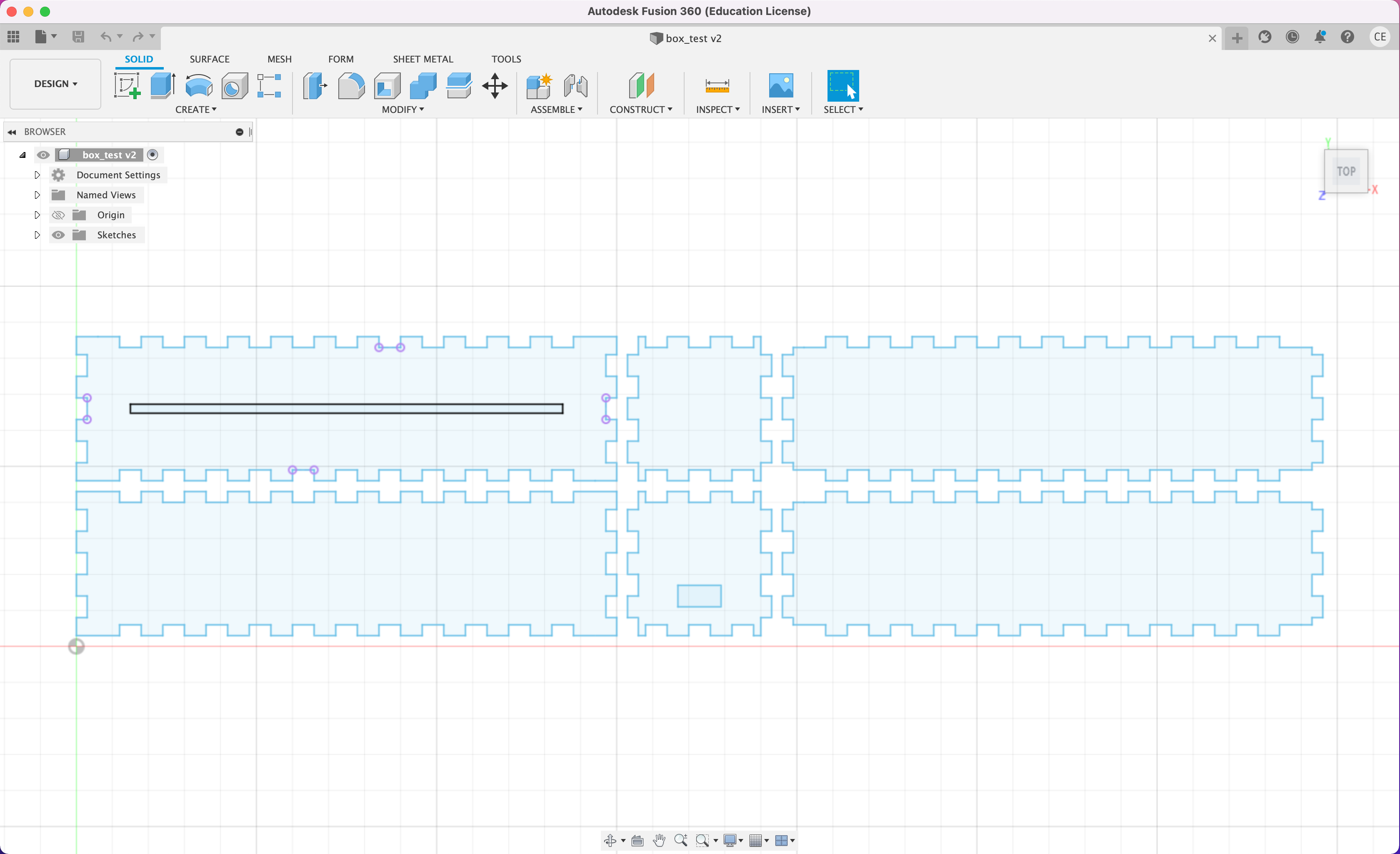
Parametric design file in Fusion 360.
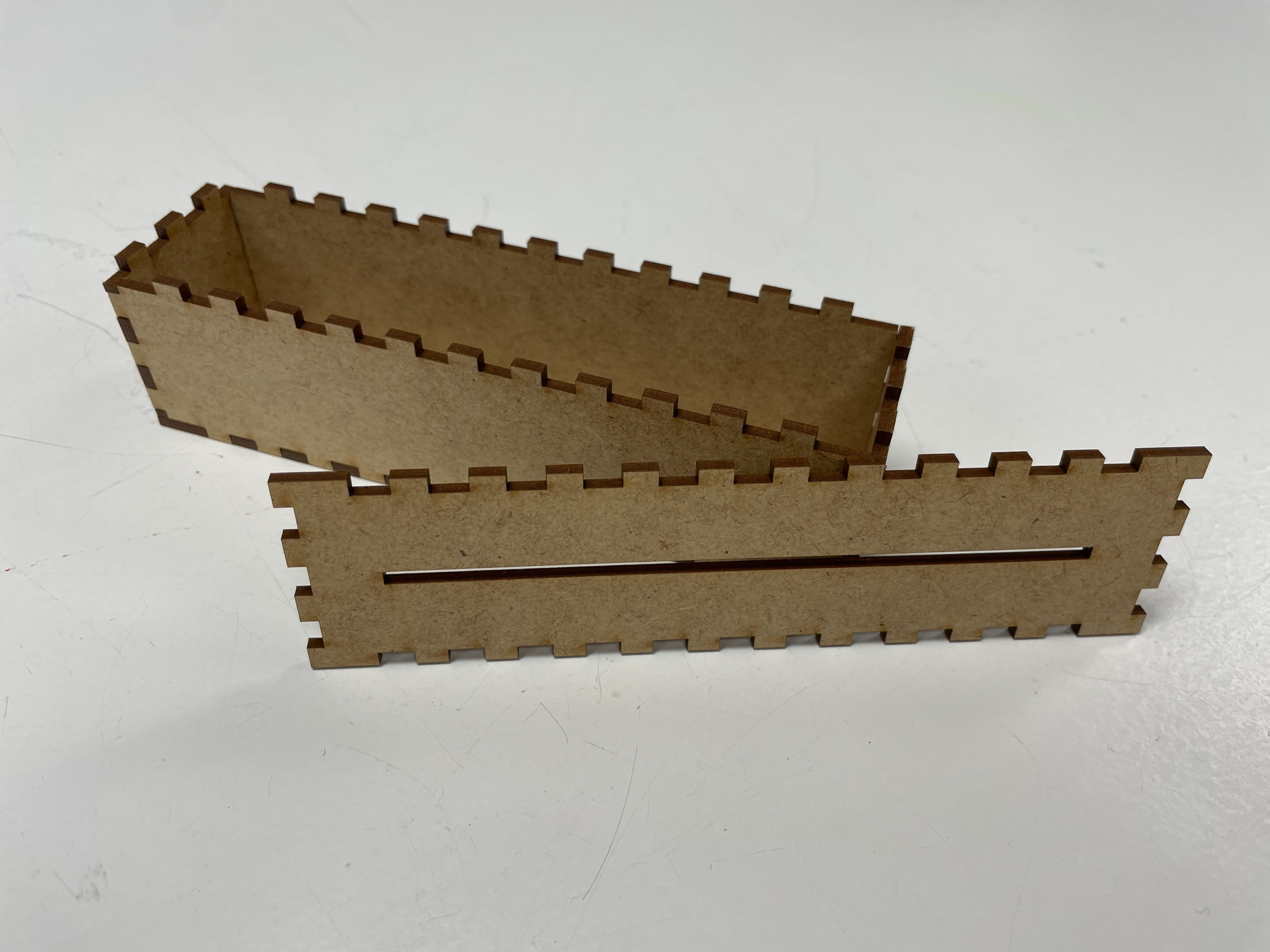
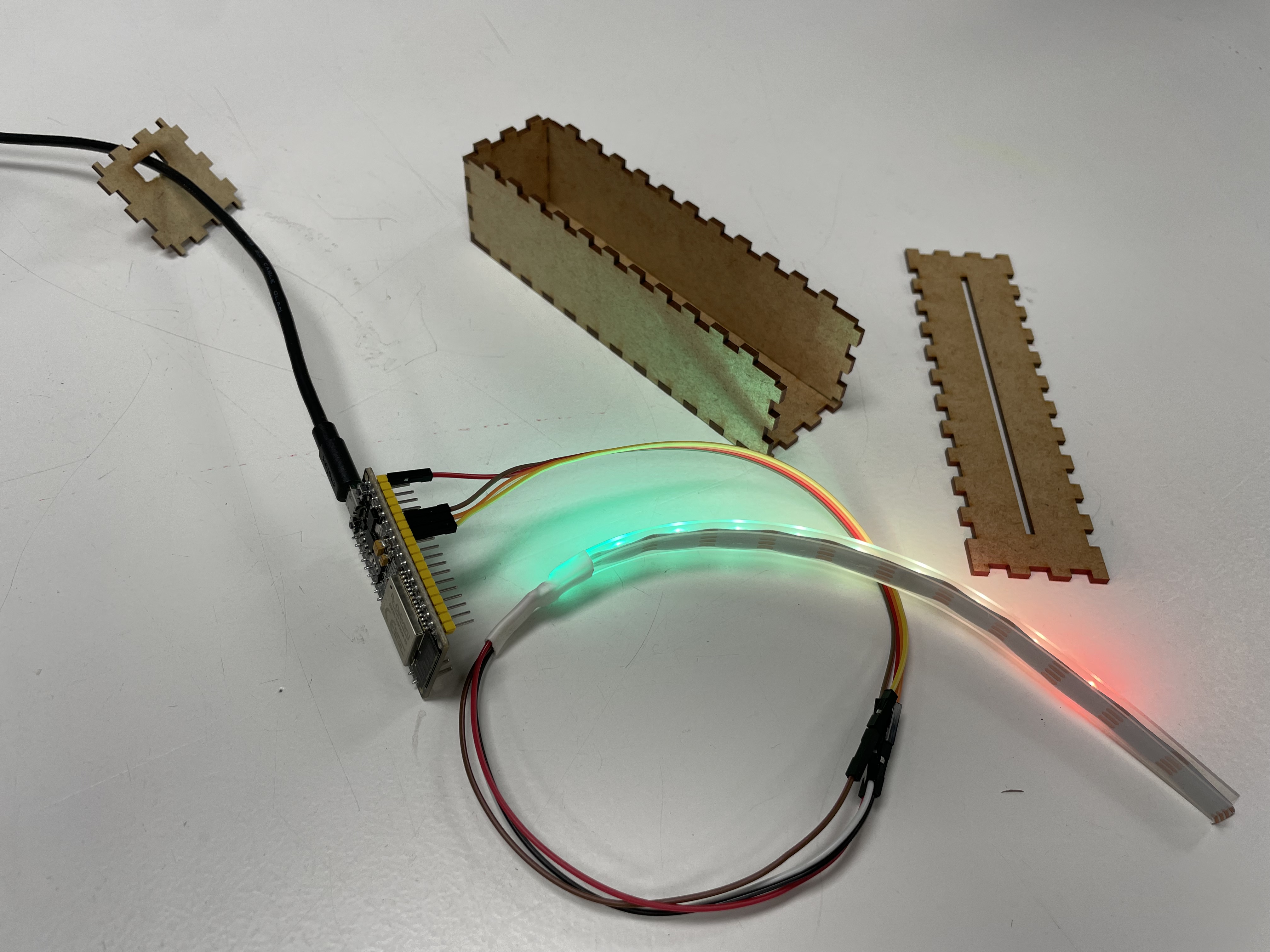
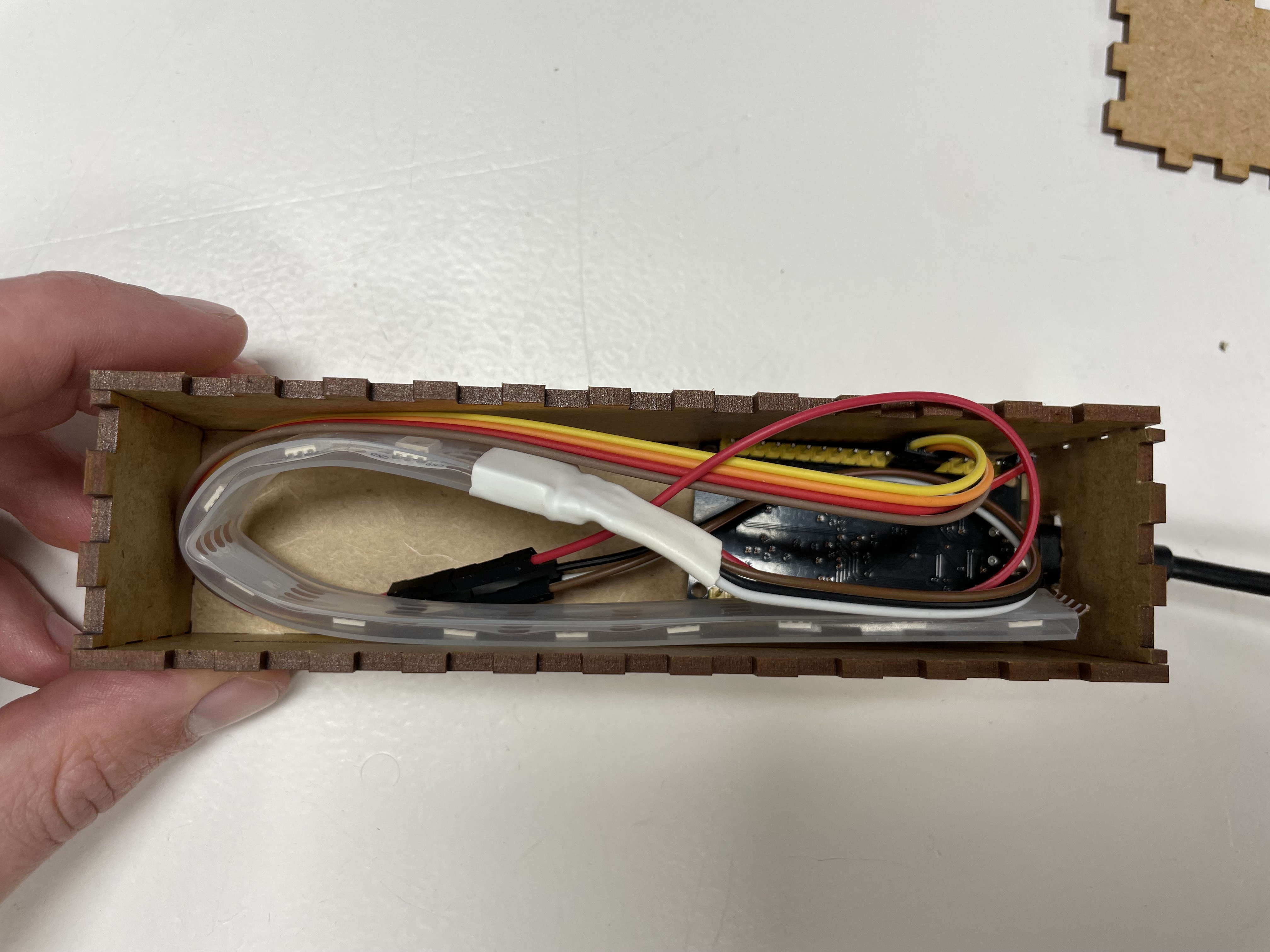
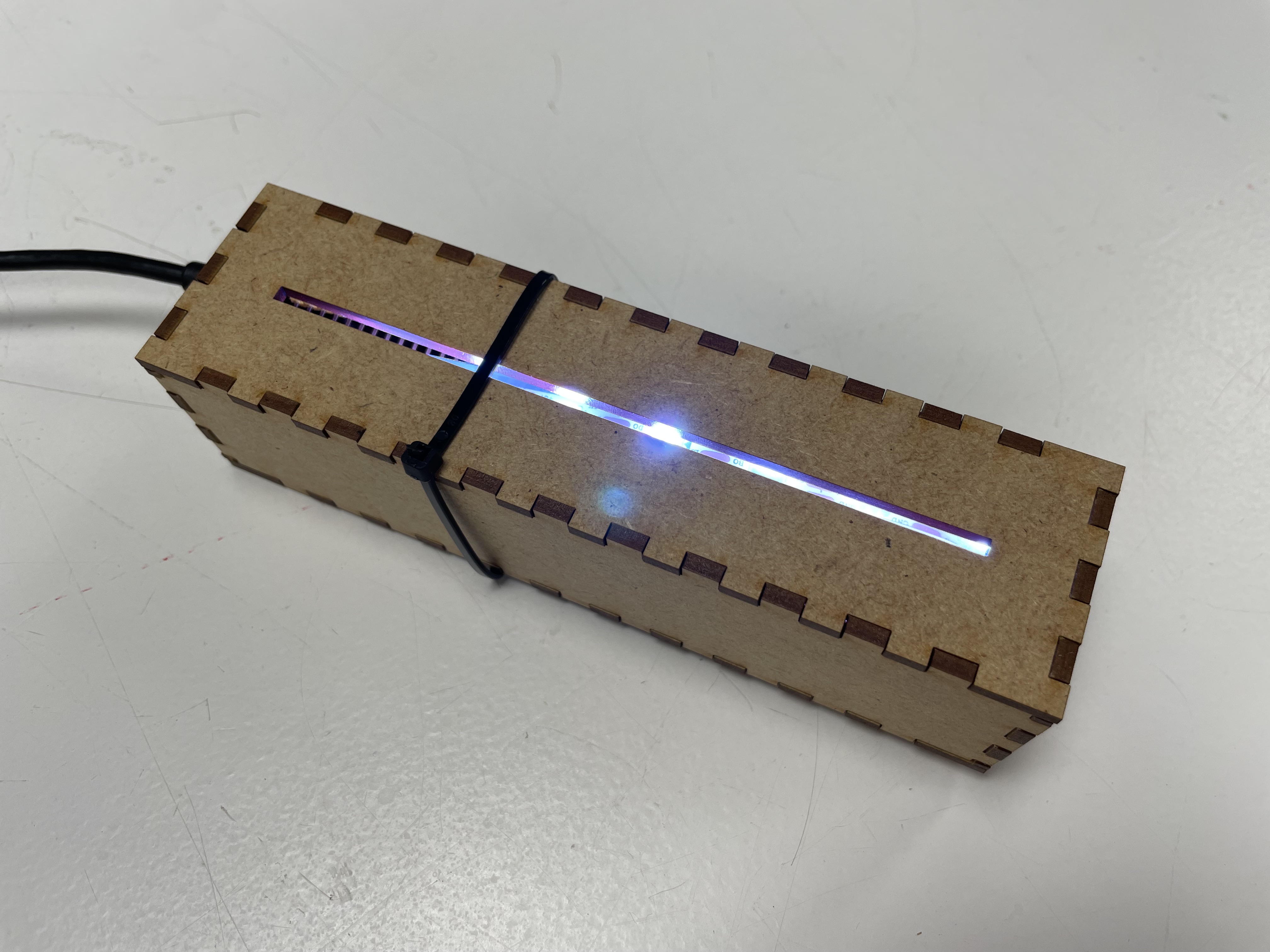
Building steps of assembling the laser-cut pieces, integrating ESP32, programming LED strip.
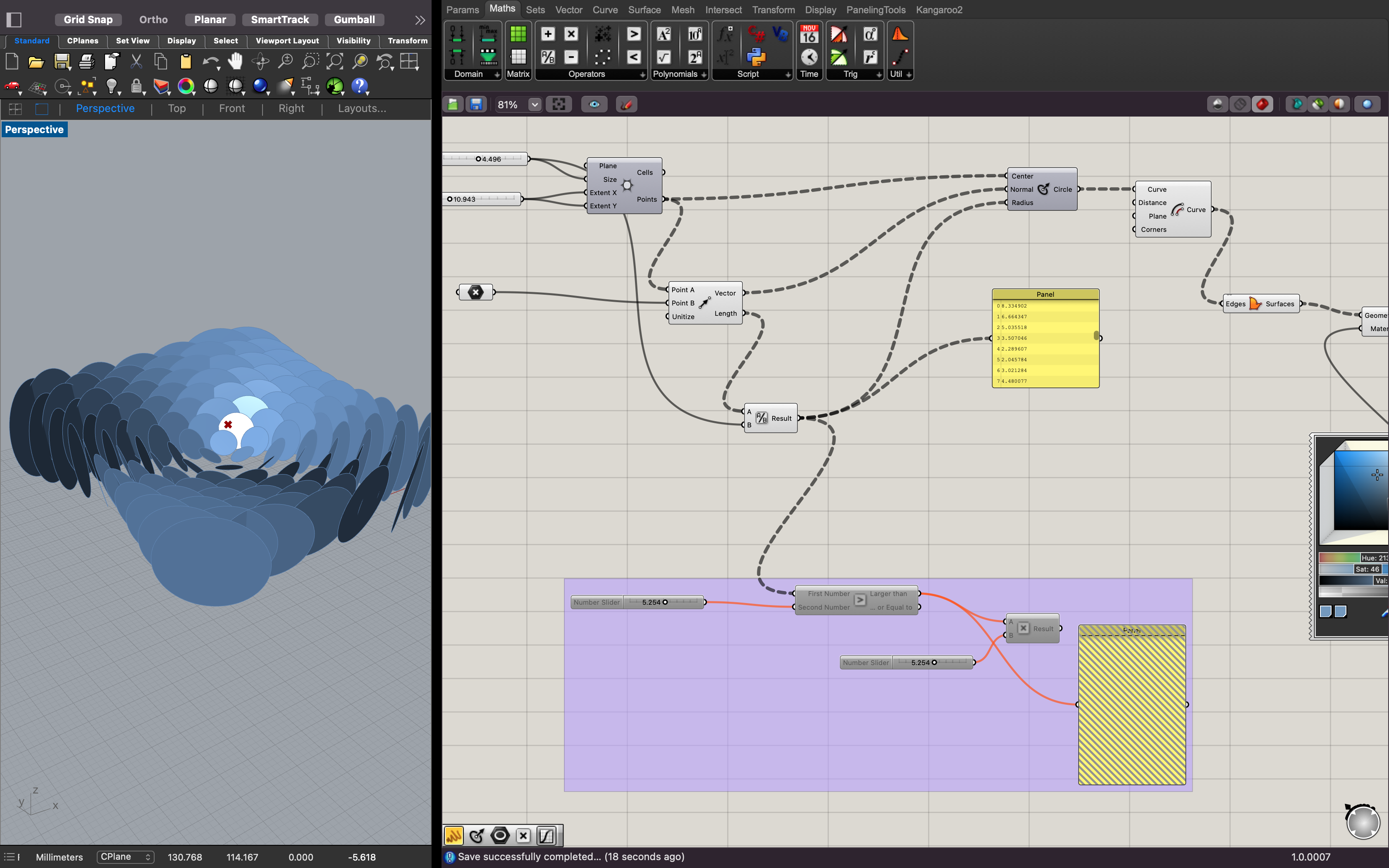
Experimenting with Grasshopper to produce an organic generative design.
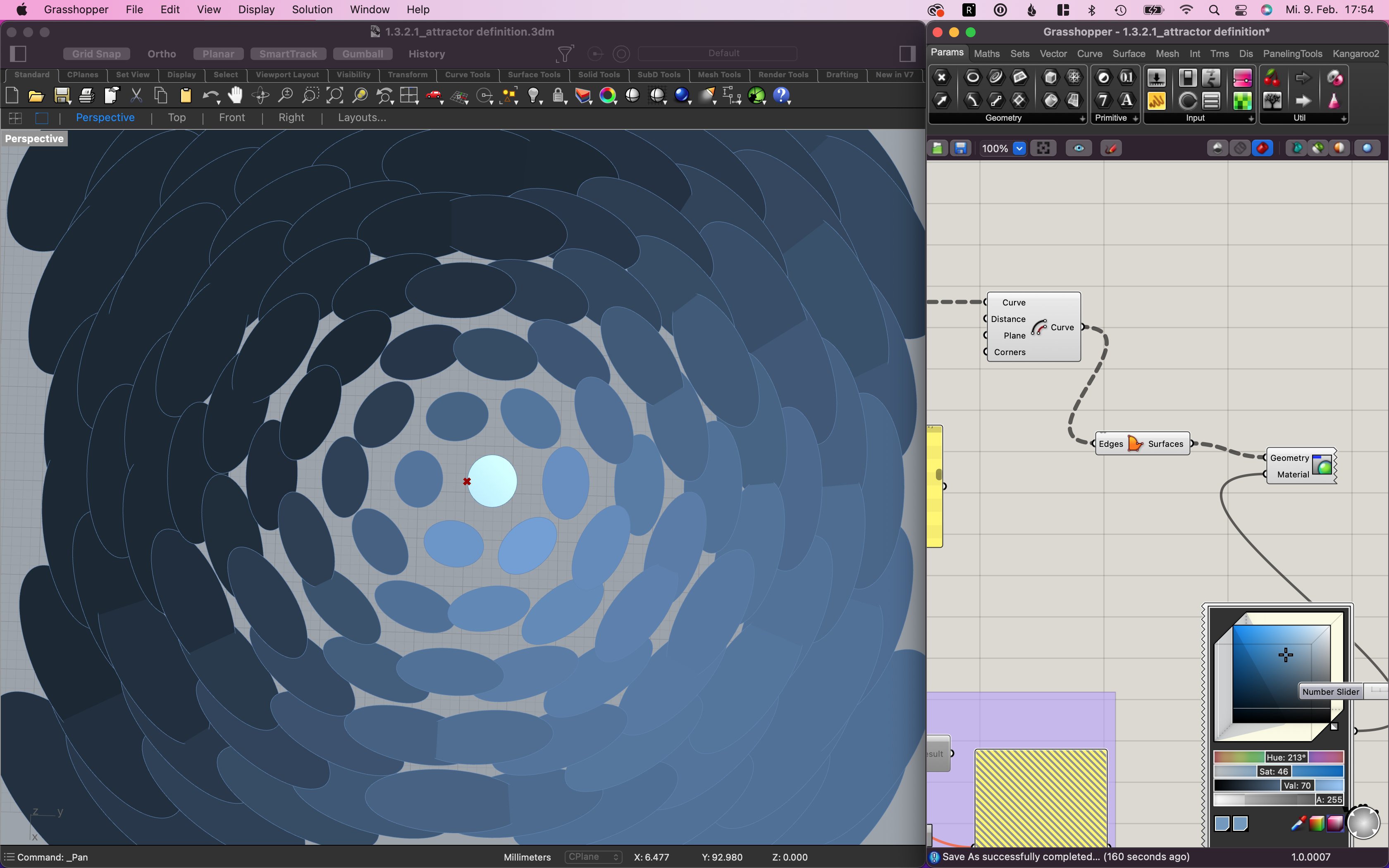
Finding a perspective to export to SVG.
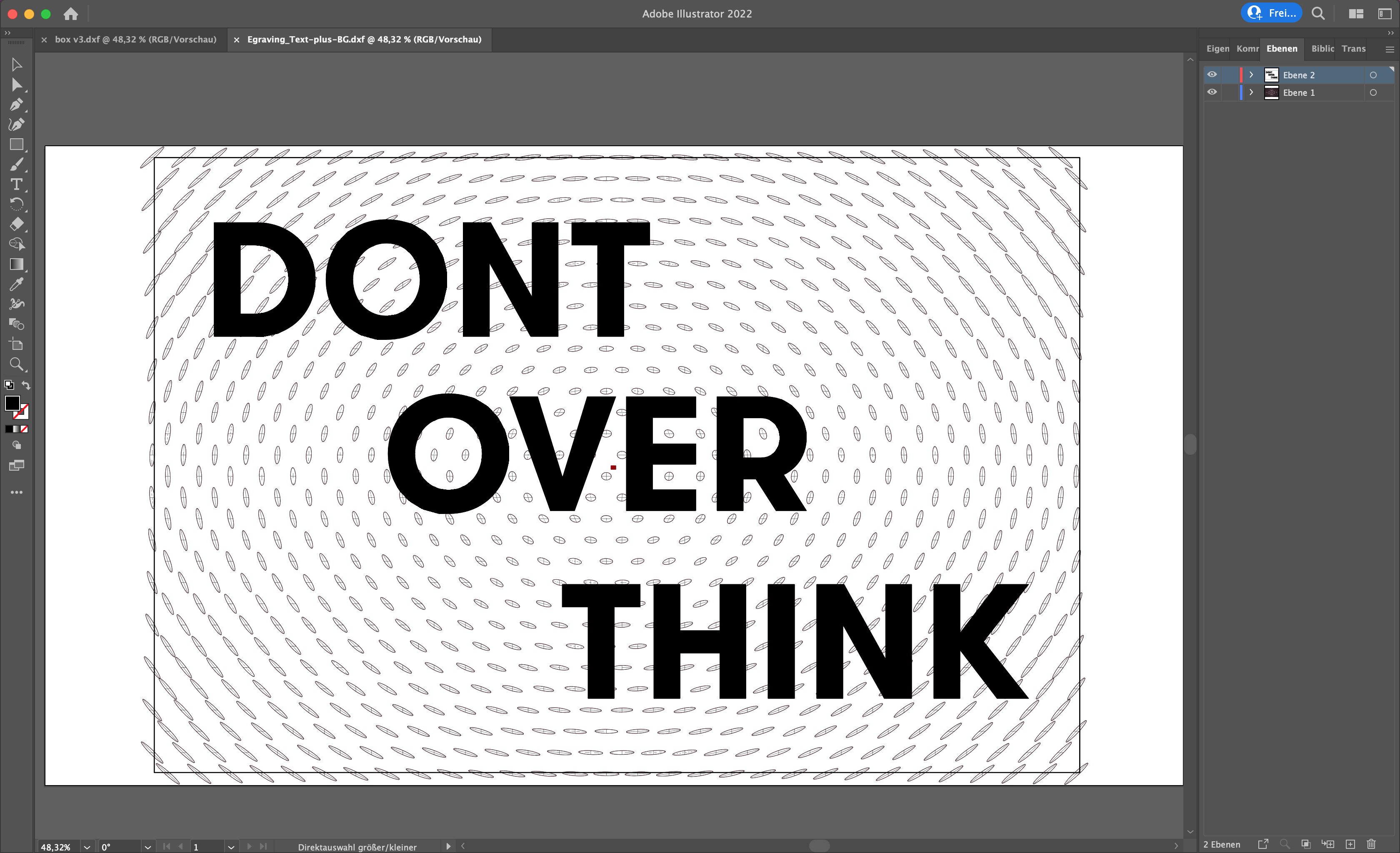
Designing the glowing sign in Illustrator to be engraved in acrylic.
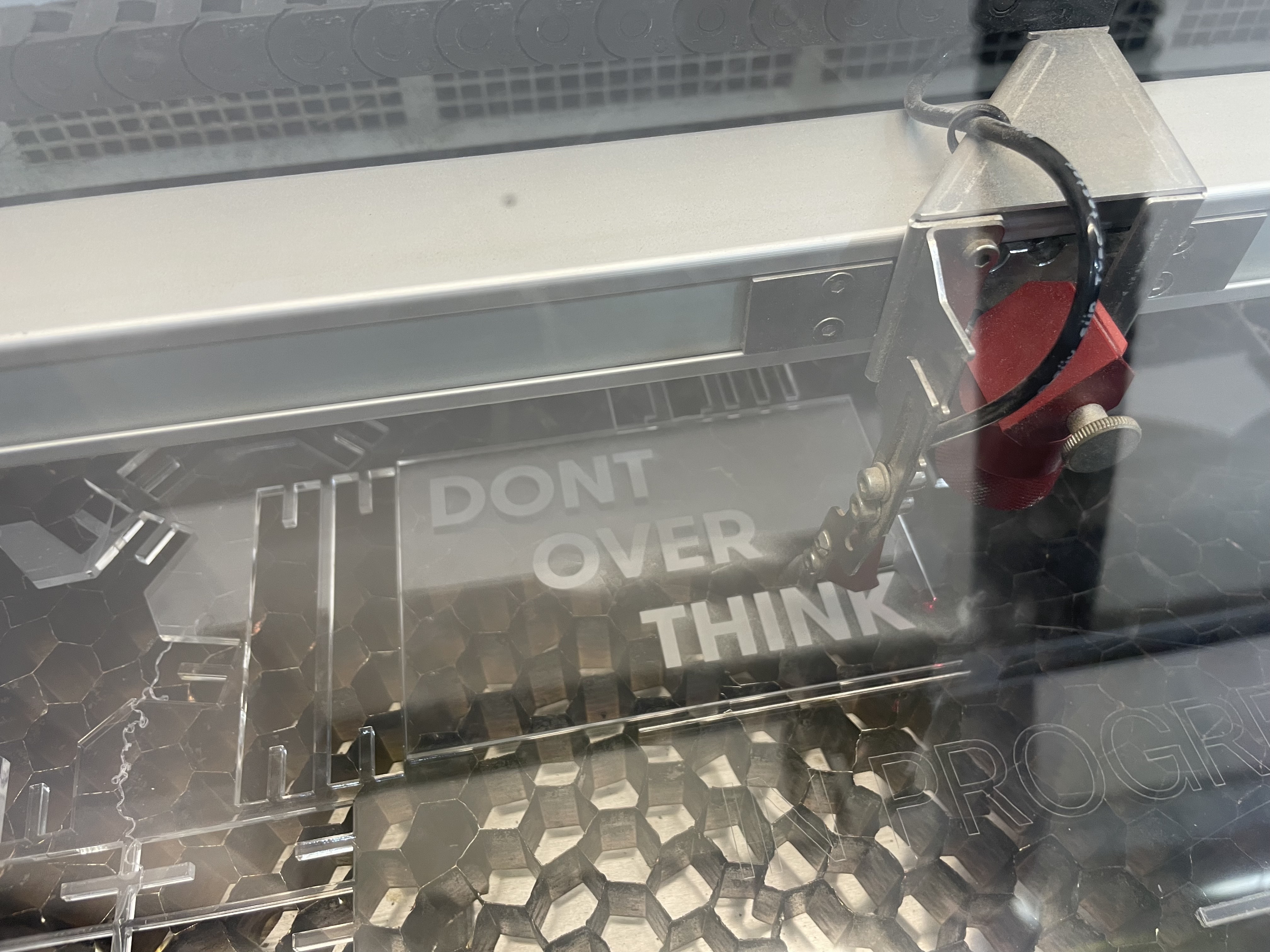
Engraving the acrylic plate in the small Trotec 100.
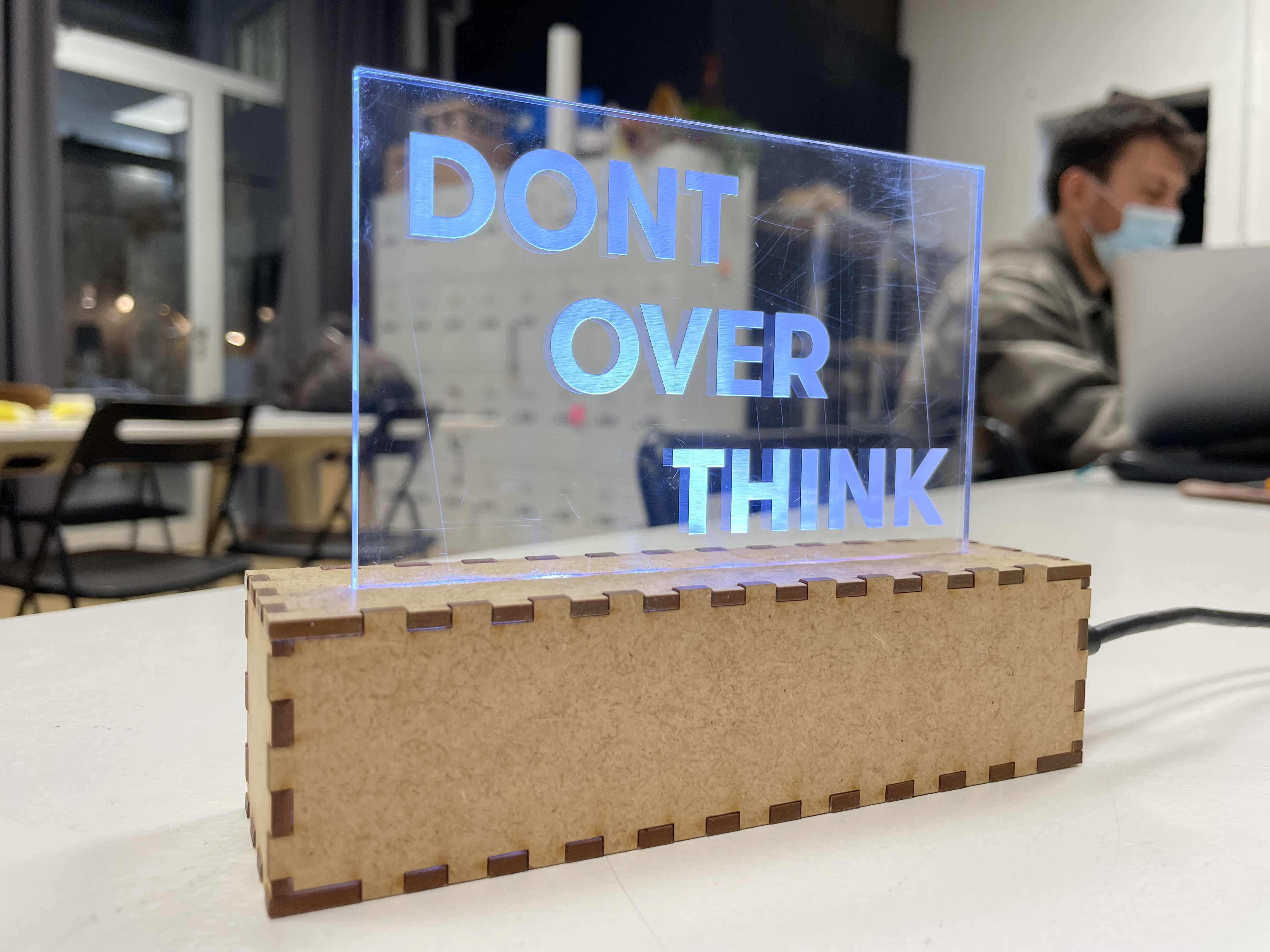
The final assembled light edge sign.
Further Links
tools
knife
Roland
Zund
Othercutter
ultrasonic
print and cut
Roland
laser
Epilog
Universal
Trotec
GCC
Full Spectrum
Lasersaur
3D FabLight
Oxford
PHAROS
plasma
Forest Scientific
Torchmate
waterjet
OMAX
Flow
WAZER
hot wire
FROGWire
Hotwire
MTM
wire EDM
Sodick
MTM
CAD
Inkscape
extensions
video
Rhino
Grasshopper
video
Blender
Sverchok
geometry nodes
FreeCAD
Sketcher
LCInterlocking
video
Fusion 360 Slicer
SolidWorks
xDesign
Onshape
Kiri:Moto
Cuttle
Kyub
Pepakura
VisiCut
flatfab
ExactFlat
CAM
printer drivers
Inkcut
Deepnest
mods
community
project
video
vinylcutter
applications
signs
thermal transfer
pop-up cards, books
origami, kirigami
screen printing
sandblasting
flex, multi-layer circuits
wiring harnesses
antennas
materials
knives
vinyl
masking tape
transfer adhesive
copper
epoxy film
sandblast stencil
settings
force
speed
cut depth
temperature, humidity, ...
rollers, feeding
weeding
adhesion
lift vs shear
lasercutter
applications
marking, engraving
raster
vector
screen printing
halftone
holes
path
app
press-fit construction
joints.FCStd
joints.png
GIK
GIK.FCStd
video
types
clearance
stress concentration
parametric design
parameter testing
living hinges, flexures, mechanisms
MEMS
Light Amplification by Stimulated Emission of Radiation
state diagram
population inversion
gain medium
lasing threshold
output coupling
beam mode, profile, waist
diffraction limit
gain medium
lifetime
CO2 (10.6 μm)
fiber (1-2 μm)
InGaAsP (1-2 μm)
AlGaAs (600-900 nm)
Nd:YAG (1064, 532 nm)
Ti:sapphire (650-1100 nm)
excimer (100-300 nm)
cutting mechanisms
burning
melting
evaporation
ablation
passes
airflow
assist
exhaust
filter
kerf
safety
classes
venting
airflow
outgassing
cleaning optics
supervision
fires
materials
cardboard
Edge Crush Test (ECT) 44
orientation
wood
custom
PMMA/acrylic/plexiglass/perspex/lucite
glue
bend
fold
POM/delrin/acetal
fabric
pasta
PVC flame test
[polycarbonate]
[metal] CerMark gypsum
settings
focus
power
speed
rate
coordinate system, origin
vector, raster
assignment
group assignment:
characterize your lasercutter's focus, power, speed, rate,
kerf, joint clearance and types
individual assignment:
cut something on the vinylcutter
design, lasercut, and document a parametric construction kit,
accounting for the lasercutter kerf,
which can be assembled in multiple ways,
and for extra credit include elements that aren't flat