About the Class
In this week's lectures, we finally dove into additive manufacturing and 3D scanning. After Edu walked us through the technical details of the process and the differences between different procedures (not all additive manufacturing is true 3D printing!), we got a hands-on introduction into preparing STL-files for printing. Further, we explored how we could use a XBox Kinect to produce a volumetric point cloud, which in turn can be converted into a mesh to be cleaned up. We were also introduced to the concept and technicalities of photogrammetry, a technique that consist of stitching together photos of a fixed object to produce a textured 3D mesh.
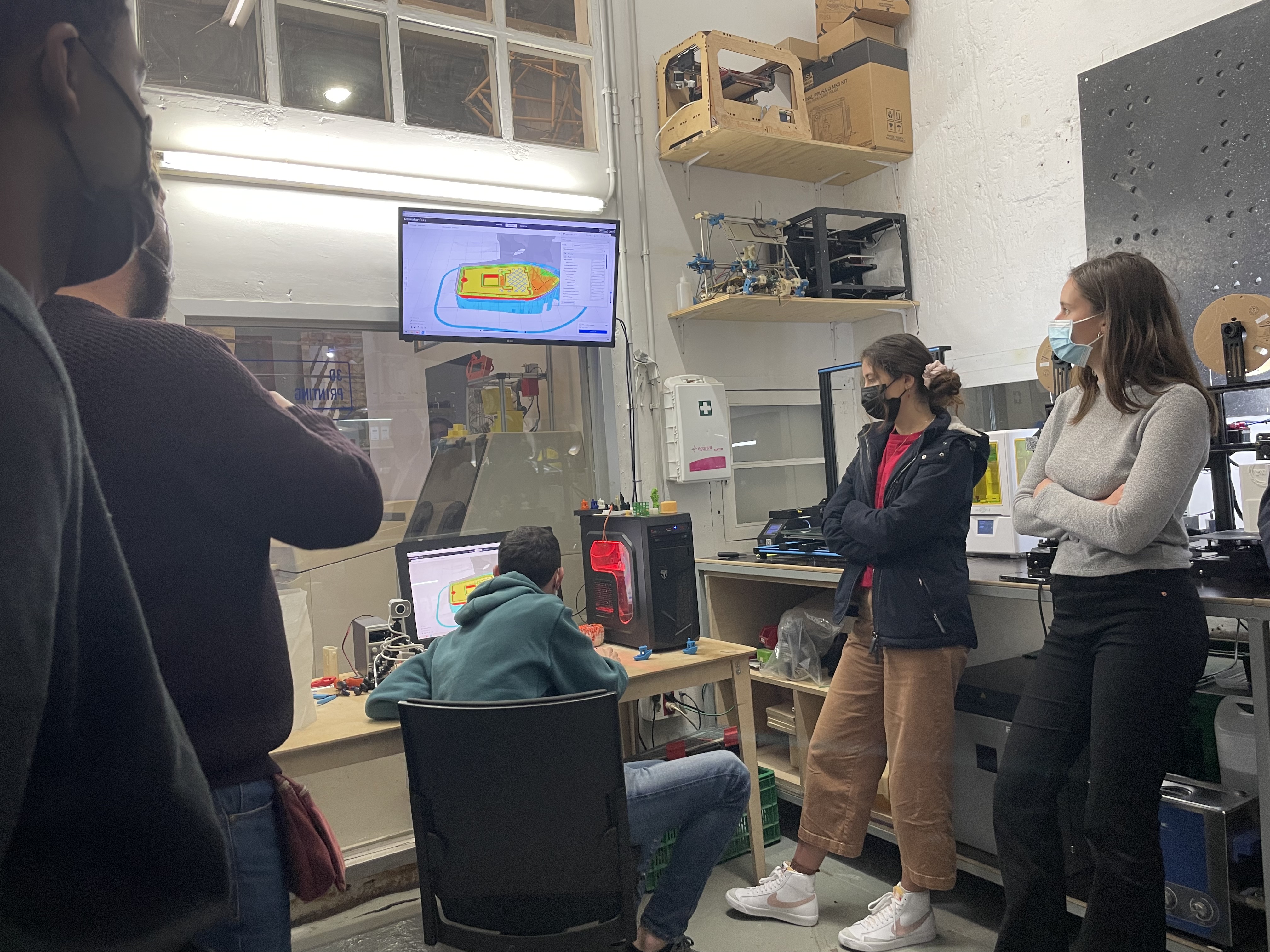
Slicing the 'benchy'' model, a small boat used for benchmarking and QA purposes, in Ultimaker Cura.
Printing a Case for my Raspberry Pi Zero
For my personal project, I decided to 3D print a custom case for my Raspberry Pi Zero. The feasibility for additive manufacturing is given here, since the object is sufficiently small, does not have a lot of volume and needs custom geometry, that would traditionally more complicated to manufacture. These were the settings used in Ultimaker Cura in preparation to print on the Creality Ender 3 Pro:
- Initial layer height 0.28 mm
- Layer height: 0.2 mm
- Printing temperature: 215 °C
- Bed heating: 60 °C
- Infill: 10 %
- Wall thickness: 2 passes
All files can be found here (click to download): Base, cover and g-code.
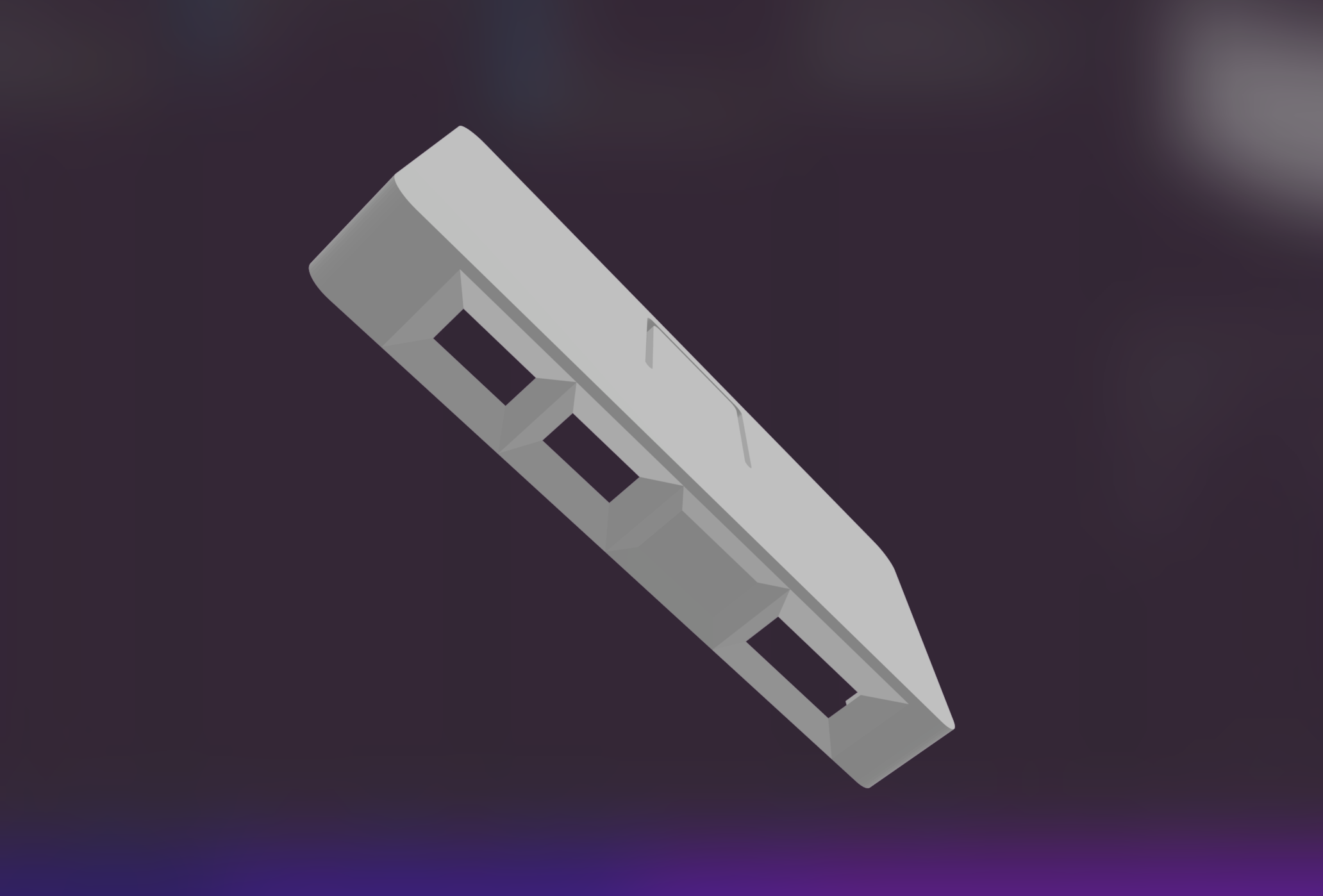
Model of the Raspberry Pi Zero.
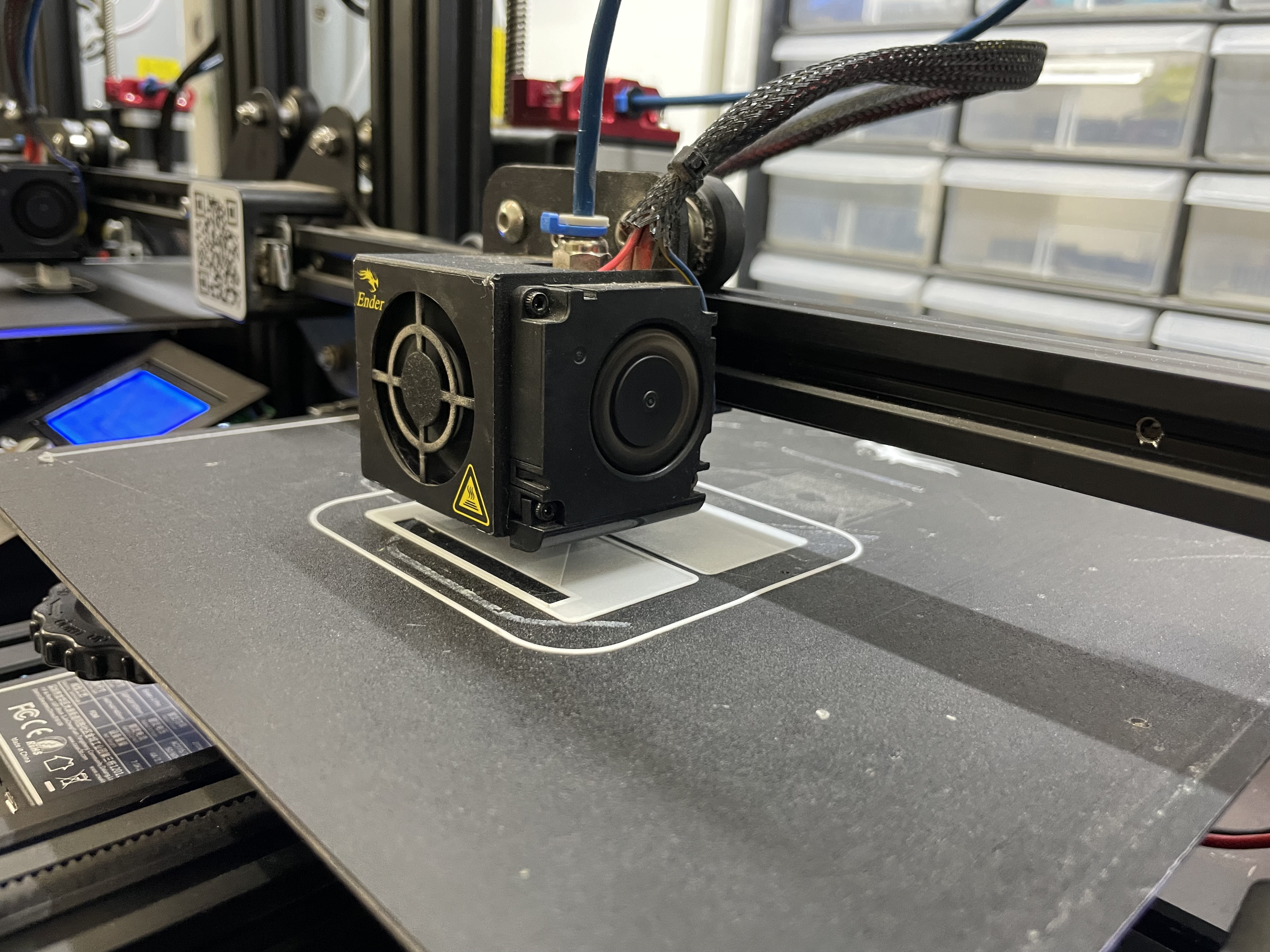
Printing in progress on the Creality Ender 3 Pro.
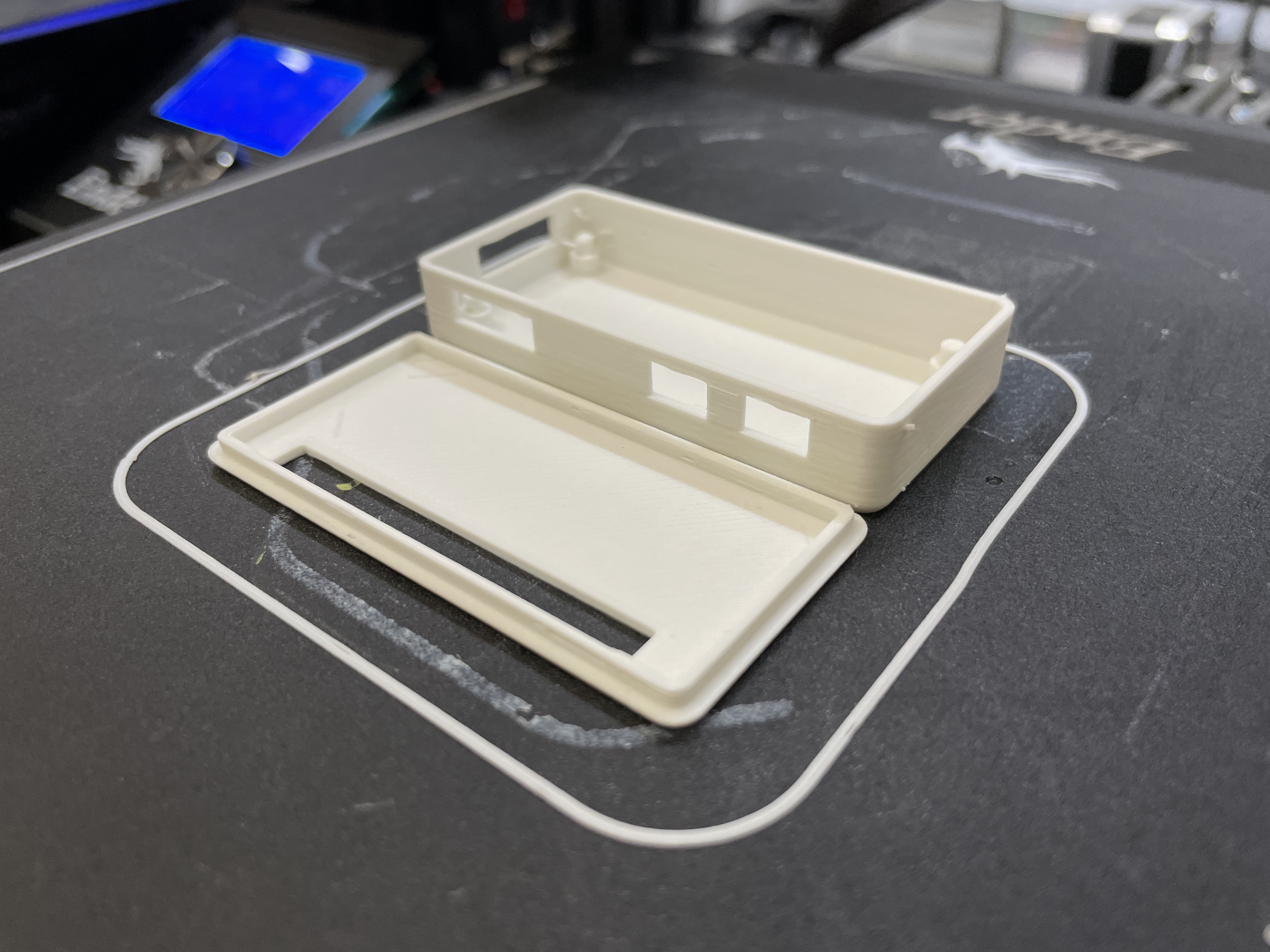
The finished print on the heating mat.
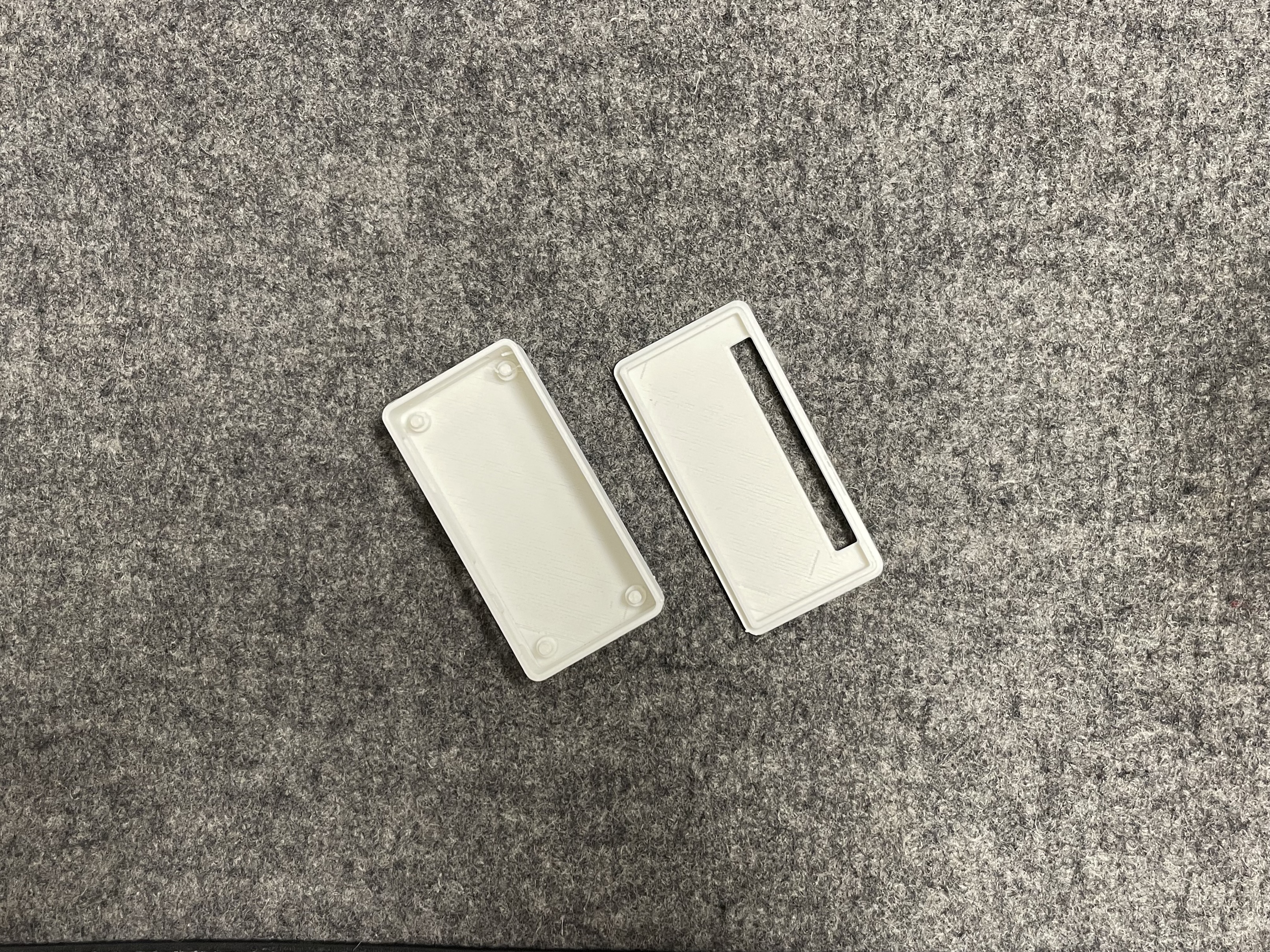
The finished pieces in a flat lay.
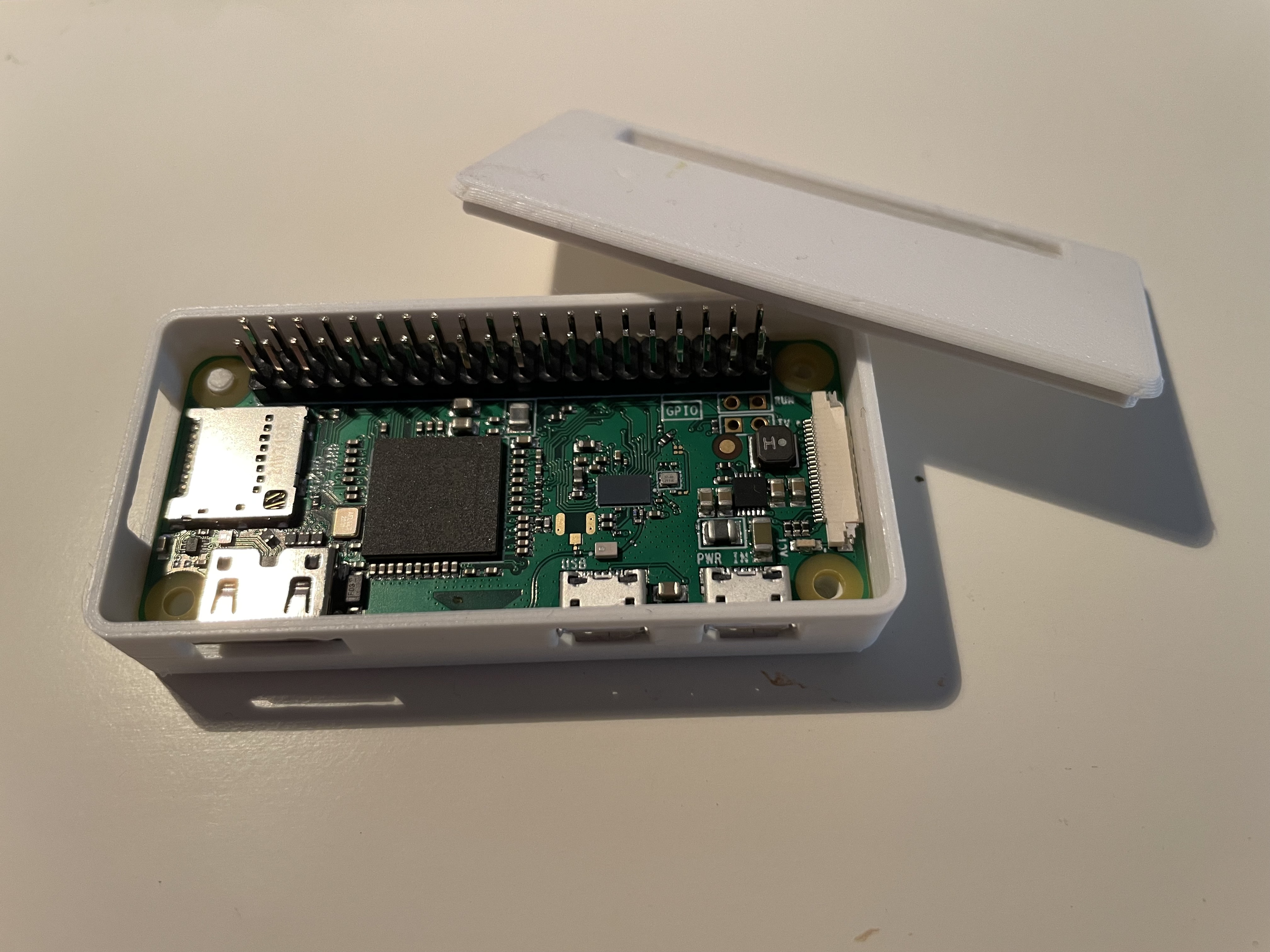
The Zero fitting snuggly into the case. I broke off three mounting pins when installing, as they were printed with hollow bases and did not withstand the pressure.
Further Links
subtractive vs
additive processes
printing
motivations
complexity
access
waste
constraints
failure
resolution
time
cost
materials
polymers: PLA, PETG, PMMA, ABS, HIPS, TPU, PVA, ...
fillers: wood, metal, ...
ventilation
design rules
supports
overhang FCStd
jpg
stl
clearance FCStd
jpg
stl
unsupported
angle FCStd
jpg
stl
overhang FCStd
jpg
stl
bridging FCStd
jpg
stl
wall thickness FCStd
jpg
stl
dimensions FCStd
jpg
stl
anisotropy FCStd
jpg
stl
surface finish FCStd
jpg
stl
infill FCStd
jpg
stl
tapers, corner
bed adhesion
post-processing
processes
stereolithography
fused-deposition molding
extrusion
contour crafting
DED, WAAM
ink-jet binder
PolyJet
cut sheets
selective laser sintering
CLIP
two photon
digital
machines
RepRap
self-replication
Ultimaker
Z-Unlimited
Prusa
MMU
parts
Sainsmart
Sindoh
Formlabs
Print the Legend
Chase Me
parts
Objet C260
parts
Stratasys J55
color
MTM
Precious Plastic
Filastruder
materials
Proto-pasta
MatterHackers
NinjaTek
The Virtual Foundry
food safety
service bureaus
print farms
Shapeways
Ponoko
Additively
file formats
ASCII
solid object_name
facet normal n1 n2 n3
outer loop
vertex v11 v12 v13
vertex v21 v22 v23
vertex v31 v32 v33
endloop
endfacet
...
endsolid object_name
binary
80 byte ASCII header
32-bit integer number of facets
50 byte facet records
32-bit IEEE floats
normal
vertices 1,2,3
2 byte attribute
right hand rule
normal (optional)
(lack of) units
PLY
AMF
3MF
FAV
OBJ, 3ds, DXF
VRML, X3D
glTF
Alembic
FREP, BREP
adaptively-sampled distance fields
volumetric
.vol, .tiff, .gif
marching cubes
fab modules vol_gif gif_stl gif_png
G-codes
non-planar paths
software
meshing
MeshLab
netfabb
meshmixer
Geomagic
slicing
ReplicatorG
Skeinforge
Slic3r
PrusaSlicer
Cura
IceSL
Kiri:Moto
printing
Printrun
OctoPrint
Repetier
sharing
Sketchfab
Thingiverse
scanning
point cloud, triangulation, watertight, texture
tomography
Radon transform
micro-CT
scanned probe
confocal
serial sections
opacity
digitizer
stereo
RealSense
LIPScan
Photogrammetry
AliceVision
Meshroom
CUDA
EC2
remote
image
ReCap
PhotoScan
VisualSFM
SCANN3D
3DSOM
Qlone
OpenMVG
COLMAP
OpenScan
speckle
OpenKinect
ReconstructMe
Skanect
laser
FabScan
structured light
laser pico-projector
Gray code
POP2
lidar
time of flight
light stage
scanning
SLAM